LBW vs GTAW: Choose the Correct Welding Method
Choosing the correct welding method can be difficult. There are several methods used during the welding process. In this article, we break down the limitations, cons, and benefits of two popular welding methods: GTAW and LBW.
Laser Beam Welding

Laser beam welding (LBW) is a process of fusing metal with an amplified beam of light. Due to its nature, there are limitations to LBW's effectiveness when welding certain materials; LBW is limited to penetration levels lower than those of TIG welding. Large gaps are difficult to fill due to the number of passes needed to fill the void.
However, the advantages of laser welding its ability to be used in assemblies that have thin-walled materials and in awkward angles. This is due to the laser beam being "shot" into deep crevices and valleys of parts.
Another benefit to LBW is that pre-assembled parts with tight function tolerances can be welded with little distortion to surrounding areas. This is an advantage over traditional TIG welding not being able to reach down into valleys in different assemblies. Laser welding can be used to weld parts that have to achieve a higher-class surface finish without having to go through an additional, external process.
Laser welding is used with welding around springs, magnets, and polymers due to the low heat output. Laser welding has a maximum filler rod thickness of .015” that can be properly used. Many parts can be welded simply by fusing both parts together in a simple fusion weld. Aluminum and magnets are not weldable within the laser welding machines.
Materials weldable by LBW:
- Stainless steels
- Low carbon steels
- Nickel-based alloys
- Titanium (refractory alloys)
- 3-D grown materials
- Cobalt
- Chromoly
- Inconel
Difficult to weld materials, or materials non-suitable for LBW:
- Brass
- Cadmium
- Zinc
- Medium-high carbon steels
- Cobalt alloys
- Copper & copper alloys
- Tungsten
- Cast iron
- Tool steels
- Aluminum
- Magnets
GTAW/TIG Welding
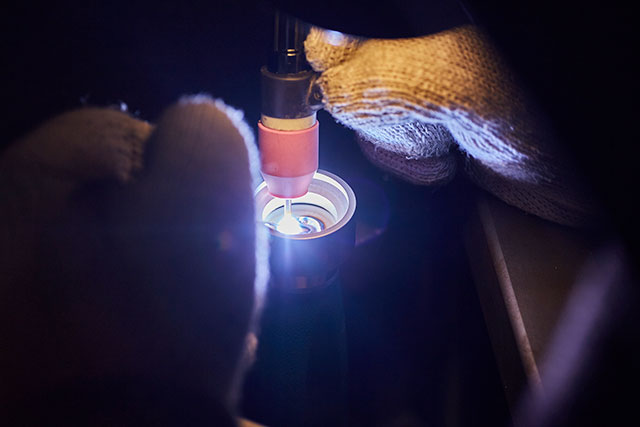
Gas tungsten arc welding (GTAW) is an arc welding process involving a non-consumable tungsten electrode to produce the weld. This process is also denominated tungsten inert gas (TIG) welding.
Unlike LBW, GTAW welding allows for deeper penetration on larger parts. It also permits larger channels and valleys to be welded due to the larger diameter of filler wire that can be used. The result is fewer passes with deeper penetration. However, parts can require pre and post heating.
The micro TIG welding process can also allow for less heat dispersion for pre-assembled parts which might contain heat sensitive components. Although, assemblies that are pre-assembled can suffer from heat distortion due to the nature of the welding process.
TIG welding is good for open weld areas that enable the electrode to be pinpointed in the desired area without it arcing out on other walls of the part. Springs and magnets are also not recommended to be welded with this process due to heat transfer possibly negatively affecting the part. Thicker materials are desired to limit burn through.
Materials commonly TIG welded:
- Stainless steels
- Aluminum
- Titanium
- Inconel
- Nickel
- Chromium-based alloys
- Low-high carbon steels
- Stellite
- Molybdenum as well as cast iron and cobalt.
- 3-D grown materials
Materials difficult to weld or non-weldable materials for GTAW:
- Zinc and its alloys
- Copper